Rewiev: 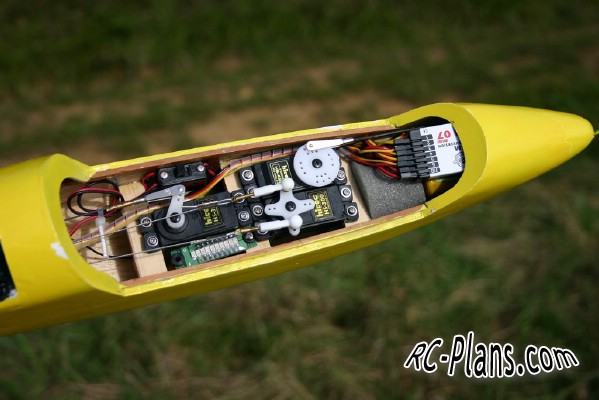
Characteristics
- Name: Entoucas
- Wingspan: 320 cm
- Length: 150 cm
- Ropes: root 20 cm, salmon 11.5 cm
- Profile: root Eppler 205, salmon Ritz 2.30.10
- Surface area: 55 dm²
- Mass: 1500 g
- Wing load: 27 g / dm²
- Equipment
- Batteries: 4.8 V 2200 mA
- Radio: 5 channels 5 servos
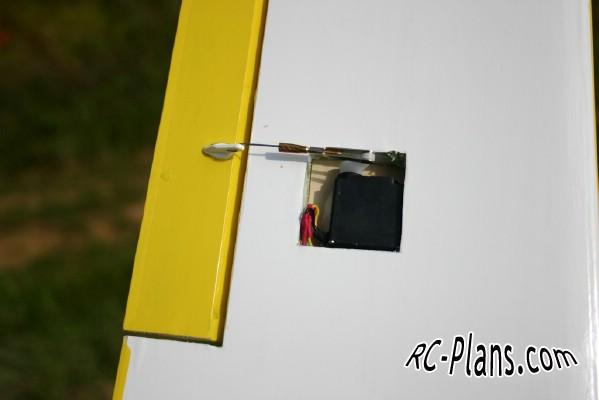
It is a perfect glider for testing slopes when the dynamics are uncertain or for flying in the lowlands.
The cell is mixed: wooden fuselage extended by a fiberglass beam, polystyrene wing boxed and empennage structure.
The particular geometry of the wing is intended to simplify the steering, especially in spiral.
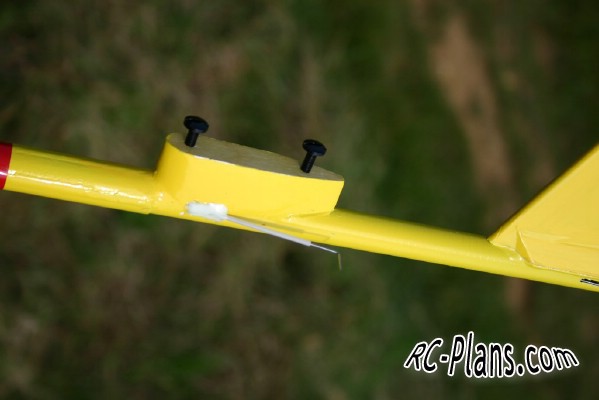
Construction
The construction itself does not pose any particular problem. Monocoque fuselage extended by a composite beam. Wing with hollow core and empennages in conventional structure. This amalgam of processes makes it possible to combine a good weight distribution and an optimized mechanical strength.
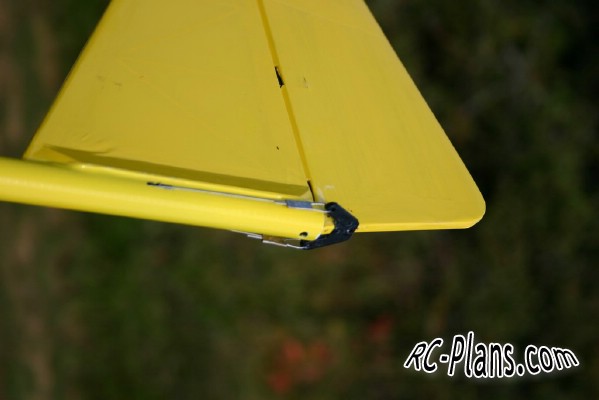
The wing
It is cut in green extruded polystyrene. Two fiberglass ties 100 g / dm² and 600 mm long are inserted on the underside and on the extrados between the core and the formwork in lightweight 15/10 balsa. Just what it takes for this to work flexibly. The root ribs are made of 30/10 plywood to take up any compression constraints (crash or hard landing). The leading edge is in 5x12 samba sticks. The wing key sleeve consists of plywood flanks enclosing a dural tube 10.5x12 in diameter and the remaining volume is filled with samba 120/10 and resin + microballoon. The wing key is carbon 10 mm over a total length of 200 mm (it is more than enough to not flutter wings in flight ...). The sheath thus produced is inserted only after the wing has been formed, by making a trench from the underside of the wing to the fiber reinforcement extrados.
The salmon are carved in a block of balsa. This wing will be held on the fuselage by M4 nylon screws. The pair of finished wing with servos and interlining weighs 780 g for 55 dm², or 14.2 g / dm². We can try to make lighter, at the risk of ending up with wing sections that are writhing with laughter at the slightest acceleration.
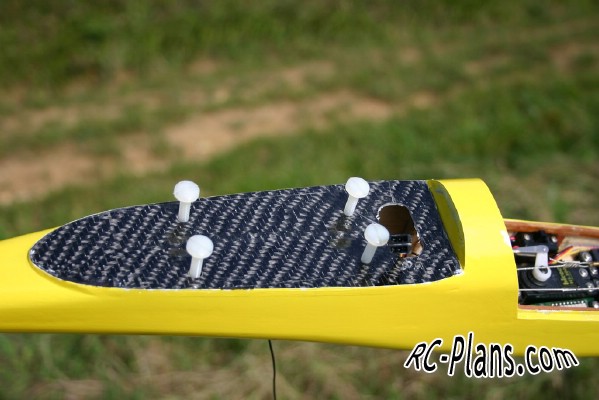
The fuselage
The construction of this centerpiece uses the technique of the monocoque structure, based on 3x10 balsa slats on degressive pairs. The fuselage is assembled in the air. So be very careful not to end up with a banana vulgar in the end. In pairs C5 and C6, arrange the composite fiber tail boom with a section of 21 to 15 mm at the ends by 1010 mm. Arrange on both sides the two sides in balsa 30/10 for the positioning of the other couples and reinforcement in 3x5 pine. Take care at this stage to identify the cutting plane of the future canopy on the sides with four holes of 1 mm at the corners. Follows the classic installation of battens 3x10 balsa. After sanding to break the rebel edges, masticate the entire shape with a Polyfilla type finish. Carry out a new sanding. Once the surface finish is right for you, rub the fuselage with two layers of fiberglass 100 g / dm² without too much resin. It is necessary to distinguish the weft after impregnation of the fabric. The excess of resin never strengthens a composite! After two days of drying, seal the fiber frame with Polyfilla plaster while taking care not to lose the canopy cutting marks. Reperce them if necessary. Sanding to a flawless surface finish.
It is time to cut the canopy using a hacksaw for the front and back, then a cutter to attack the horizontal parts by making several passes in the material. It's not very difficult, but it takes a little patience and care if you do not want to have to repair the crevices. Normally the canopy should come off without a hint if you have taken care not to stick together the C2 / C2bis and C3 / C3bis assembly torques.
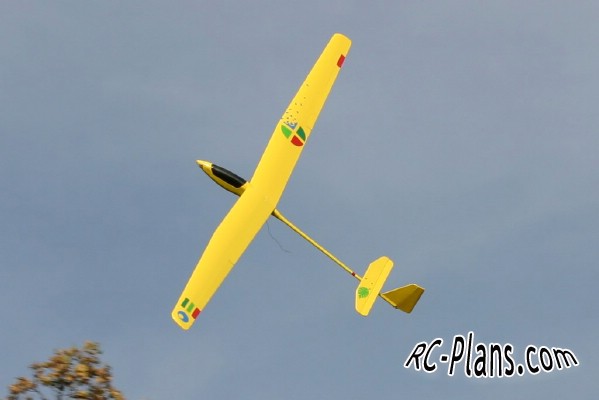
The empennages
The stab and the drift are made in balsa structure. The profiles are plank type for reasons of simplicity and speed of construction. I am personally convinced that the use of true symmetrical profiles greatly improves the aerodynamic efficiency, whether or not it is deflected (dynamic damping).
The movable shutters are cut in a board of 50/10 light balsa. The trailing edges are formed in the same "metal", we can not do more simple and lightweight. For example, the finished stab and fabric weighs 32 g, for 6.45 dm² of surface, which gives less than 5 g / dm²! Even in any plastic one could not get such a result without the risk of having the impression of handling frail butterfly wings. This is not the same surface, you will agree!
The stab mast is drawn from a laminating of 2 layers of 80/10 balsa. It encloses M4 nuts under its 10/10 plywood plate.
To facilitate its bonding on the fuselage, it will be bolted to the stab and presented in this way when the time comes.
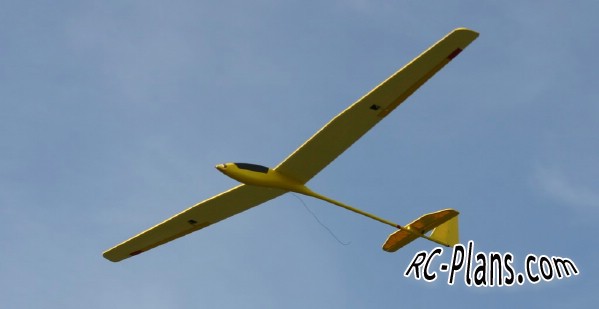
To compensate for the day of the saw blade, make in 10/10 plywood two small frames of 10 mm wide which will considerably strengthen the fuselage in line with this opening. Keep the canopy as it is, or else you can make a master to mold a canopy in Rhodoïd, or for the chic side why not carbon? In the fuselage, remove the pairs C2 bis and C3 bis construction, then rub the entire interior between C1 and C4 with a layer of fiberglass 100 g / dm². Glue the wing support plates. The seat of the wing is directly molded on the wing itself, applying a layer of carbon 200 g / dm² of 22x10 cm. We first prepared the surface with packing tape, a little release agent and we go cheerfully. Once dry, do not take off, drill with a 4 mm drill the passage of the wing fixing screws through all the elements. Present the wing on the fuselage and drill the supports using the holes in the wing. Put in place the claw nuts. Then proceed to glue the whole epoxy 15 minutes using the M4 fastening screws for tightening. Make sure that the whole thing is symmetrical. While everything is immobilized, empennages can be reported according to plan.
Finally, after dismounting the wing fixing screws, unmold with a sharp blow. Normally the wing must separate from the fuselage. Otherwise you will have to tear down the partitions of your workshop to get out and probably invest in a new means of locomotion to get to the field with your artwork! In short, clear everything that goes beyond the fuselage. Is not it beautiful this fuselage molded? Come on, wipe away your tears of emotion and move on.
Finish
No miracle solution for Entoucas, it will be fast: the fuselage receives a coat of apron and two layers of paint without further process, while the half-wings and empennages are simply lined with film heat-shrinkable Oracover. We can not do faster.